Low Cost Housing
Low Cost Housing is a new concept which deals with effective budgeting and following of techniques which help in reducing the cost construction through the use of locally available materials along with improved skills and technology without sacrificing the strength, performance and life of the structure.There is huge misconception that low cost housing is suitable for only sub standard works and they are constructed by utilizing cheap building materials of low quality.The fact is that Low cost housing is done by proper management of resources.Economy is also achieved by postponing finishing works or implementing them in phases.
Building Cost
The building construction cost can be divided into two parts namely:
Building material cost : 65 to 70 %
Labour cost : 65 to 70 %
Now in low cost housing, building material cost is less because we make use of the locally available materials and also the labour cost can be reduced by properly making the time schedule of our work. Cost of reduction is achieved by selection of more efficient material or by an improved design.
Areas from where cost can be reduced are:-
1) Reduce plinth area by using thinner wall concept.Ex.15 cms thick solid concrete block wall.
The building construction cost can be divided into two parts namely:
Building material cost : 65 to 70 %
Labour cost : 65 to 70 %
Now in low cost housing, building material cost is less because we make use of the locally available materials and also the labour cost can be reduced by properly making the time schedule of our work. Cost of reduction is achieved by selection of more efficient material or by an improved design.
Areas from where cost can be reduced are:-
1) Reduce plinth area by using thinner wall concept.Ex.15 cms thick solid concrete block wall.
2) Use locally available material in an innovative form like soil cement blocks in place of burnt brick.
3) Use energy efficiency materials which consumes less energy like concrete block in place of burnt brick.
4) Use environmentally friendly materials which are substitute for conventional building components like use R.C.C. Door and window frames in place of wooden frames.
5) Preplan every component of a house and rationalize the design procedure for reducing the size of the component in the building.
6) By planning each and every component of a house the wastage of materials due to demolition of the unplanned component of the house can be avoided.
7) Each component of the house shall be checked whether if it’s necessary, if it is not necessary, then that component should not be used.
Cost reduction through adhoc methods
Foundation
Normally the foundation cost comes to about 10 to 15% of the total building and usually foundation depth of 3 to 4 ft. is adopted for single or double store building and also the concrete bed of 6″(15 Cms.) is used for the foundation which could be avoided.
Foundation
Normally the foundation cost comes to about 10 to 15% of the total building and usually foundation depth of 3 to 4 ft. is adopted for single or double store building and also the concrete bed of 6″(15 Cms.) is used for the foundation which could be avoided.
It is recommended to adopt a foundation depth of 2 ft.(0.6m) for normal soil like gravely soil, red soils etc., and use the uncoursed rubble masonry with the bond stones and good packing. Similarly the foundation width is rationalized to 2 ft.(0.6m).To avoid cracks formation in foundation the masonry shall be thoroughly packed with cement mortar of 1:8 boulders and bond stones at regular intervals.
It is further suggested adopt arch foundation in ordinary soil for effecting reduction in construction cost up to 40%.This kind of foundation will help in bridging the loose pockets of soil which occurs along the foundation.
It is further suggested adopt arch foundation in ordinary soil for effecting reduction in construction cost up to 40%.This kind of foundation will help in bridging the loose pockets of soil which occurs along the foundation.
In the case black cotton and other soft soils it is recommend to use under ream pile foundation which saves about 20 to 25% in cost over the conventional method of construction.
Plinth
It is suggested to adopt 1 ft. height above ground level for the plinth and may be constructed with a cement mortar of 1:6. The plinth slab of 4 to 6″ which is normally adopted can be avoided and in its place brick on edge can be used for reducing the cost. By adopting this procedure the cost of plinth foundation can be reduced by about 35 to 50%.It is necessary to take precaution of providing impervious blanket like concrete slabs or stone slabs all round the building for enabling to reduce erosion of soil and thereby avoiding exposure of foundation surface and crack formation.
It is suggested to adopt 1 ft. height above ground level for the plinth and may be constructed with a cement mortar of 1:6. The plinth slab of 4 to 6″ which is normally adopted can be avoided and in its place brick on edge can be used for reducing the cost. By adopting this procedure the cost of plinth foundation can be reduced by about 35 to 50%.It is necessary to take precaution of providing impervious blanket like concrete slabs or stone slabs all round the building for enabling to reduce erosion of soil and thereby avoiding exposure of foundation surface and crack formation.
Walling
Wall thickness of 6 to 9″ is recommended for adoption in the construction of walls all-round the building and 41/2 ” for inside walls. It is suggested to use burnt bricks which are immersed in water for 24 hours and then shall be used for the walls
Wall thickness of 6 to 9″ is recommended for adoption in the construction of walls all-round the building and 41/2 ” for inside walls. It is suggested to use burnt bricks which are immersed in water for 24 hours and then shall be used for the walls
Rat – trap bond wall
It is a cavity wall construction with added advantage of thermal comfort and reduction in the quantity of bricks required for masonry work. By adopting this method of bonding of brick masonry compared to traditional English or Flemish bond masonry, it is possible to reduce in the material cost of bricks by 25% and about 10to 15% in the masonry cost. By adopting rat-trap bond method one can create aesthetically pleasing wall surface and plastering can be avoided.
It is a cavity wall construction with added advantage of thermal comfort and reduction in the quantity of bricks required for masonry work. By adopting this method of bonding of brick masonry compared to traditional English or Flemish bond masonry, it is possible to reduce in the material cost of bricks by 25% and about 10to 15% in the masonry cost. By adopting rat-trap bond method one can create aesthetically pleasing wall surface and plastering can be avoided.
Concrete block walling
In view of high energy consumption by burnt brick it is suggested to use concrete block (block hollow and solid) which consumes about only 1/3 of the energy of the burnt bricks in its production. By using concrete block masonry the wall thickness can be reduced from 20 cms to 15 Cms. Concrete block masonry saves mortar consumption, speedy construction of wall resulting in higher output of labour, plastering can be avoided thereby an overall saving of 10 to 25% can be achieved.
In view of high energy consumption by burnt brick it is suggested to use concrete block (block hollow and solid) which consumes about only 1/3 of the energy of the burnt bricks in its production. By using concrete block masonry the wall thickness can be reduced from 20 cms to 15 Cms. Concrete block masonry saves mortar consumption, speedy construction of wall resulting in higher output of labour, plastering can be avoided thereby an overall saving of 10 to 25% can be achieved.
Soil cement block technology
It is an alternative method of construction of walls using soil cement blocks in place of burnt bricks masonry. It is an energy efficient method of construction where soil mixed with 5% and above cement and pressed in hand operated machine and cured well and then used in the masonry. This masonry doesn’t require plastering on both sides of the wall. The overall economy that could be achieved with the soil cement technology is about 15 to 20% compared to conventional method of construction.
It is an alternative method of construction of walls using soil cement blocks in place of burnt bricks masonry. It is an energy efficient method of construction where soil mixed with 5% and above cement and pressed in hand operated machine and cured well and then used in the masonry. This masonry doesn’t require plastering on both sides of the wall. The overall economy that could be achieved with the soil cement technology is about 15 to 20% compared to conventional method of construction.
Doors and windows
It is suggested not to use wood for doors and windows and in its place concrete or steel section frames shall be used for achieving saving in cost up to 30 to 40%.Similiarly for shutters commercially available block boards, fibre or wooden practical boards etc., shall be used for reducing the cost by about 25%.By adopting brick jelly work and precast components effective ventilation could be provided to the building and also the construction cost could be saved up to 50% over the window components.
It is suggested not to use wood for doors and windows and in its place concrete or steel section frames shall be used for achieving saving in cost up to 30 to 40%.Similiarly for shutters commercially available block boards, fibre or wooden practical boards etc., shall be used for reducing the cost by about 25%.By adopting brick jelly work and precast components effective ventilation could be provided to the building and also the construction cost could be saved up to 50% over the window components.
Lintals and Chajjas
The traditional R.C.C. lintels which are costly can be replaced by brick arches for small spans and save construction cost up to 30 to 40% over the traditional method of construction. By adopting arches of different shapes a good architectural pleasing appearance can be given to the external wall surfaces of the brick masonry.
The traditional R.C.C. lintels which are costly can be replaced by brick arches for small spans and save construction cost up to 30 to 40% over the traditional method of construction. By adopting arches of different shapes a good architectural pleasing appearance can be given to the external wall surfaces of the brick masonry.
Roofing
Normally 5″(12.5 cms) thick R.C.C. slabs is used for roofing of residential buildings. By adopting rationally designed insitu construction practices like filler slab and precast elements the construction cost of roofing can be reduced by about 20 to 25%.
Normally 5″(12.5 cms) thick R.C.C. slabs is used for roofing of residential buildings. By adopting rationally designed insitu construction practices like filler slab and precast elements the construction cost of roofing can be reduced by about 20 to 25%.
Filler slabs
They are normal RCC slabs where bottom half (tension) concrete portions are replaced by filler materials such as bricks, tiles, cellular concrete blocks, etc.These filler materials are so placed as not to compromise structural strength, result in replacing unwanted and nonfunctional tension concrete, thus resulting in economy. These are safe, sound and provide aesthetically pleasing pattern ceilings and also need no plaster.
They are normal RCC slabs where bottom half (tension) concrete portions are replaced by filler materials such as bricks, tiles, cellular concrete blocks, etc.These filler materials are so placed as not to compromise structural strength, result in replacing unwanted and nonfunctional tension concrete, thus resulting in economy. These are safe, sound and provide aesthetically pleasing pattern ceilings and also need no plaster.
For more on filler materials check Filler Materials Used in Concrete
Jack arch roof/floor
They are easy to construct, save on cement and steel, are more appropriate in hot climates. These can be constructed using compressed earth blocks also as alternative to bricks for further economy.
They are easy to construct, save on cement and steel, are more appropriate in hot climates. These can be constructed using compressed earth blocks also as alternative to bricks for further economy.
Ferrocement channel/shell unit
Provide an economic solution to RCC slab by providing 30 to 40% cost reduction on floor/roof unit over RCC slabs without compromising the strength. These being precast, construction is speedy, economical due to avoidance of shuttering and facilitate quality control.
Provide an economic solution to RCC slab by providing 30 to 40% cost reduction on floor/roof unit over RCC slabs without compromising the strength. These being precast, construction is speedy, economical due to avoidance of shuttering and facilitate quality control.
Finishing Work
The cost of finishing items like sanitary, electricity, painting etc., varies depending upon the type and quality of products used in the building and its cost reduction is left to the individual choice and liking.
The cost of finishing items like sanitary, electricity, painting etc., varies depending upon the type and quality of products used in the building and its cost reduction is left to the individual choice and liking.
Conclusion
The above list of suggestion for reducing construction cost is of general nature and it varies depending upon the nature of the building to be constructed, budget of the owner, geographical location where the house is to be constructed, availability of the building material, good construction management practices etc. However it is necessary that good planning and design methods shall be adopted by utilizing the services of an experienced engineer or an architect for supervising the work, thereby achieving overall cost effectiveness to the extent of 25% in actual practice.
The above list of suggestion for reducing construction cost is of general nature and it varies depending upon the nature of the building to be constructed, budget of the owner, geographical location where the house is to be constructed, availability of the building material, good construction management practices etc. However it is necessary that good planning and design methods shall be adopted by utilizing the services of an experienced engineer or an architect for supervising the work, thereby achieving overall cost effectiveness to the extent of 25% in actual practice.
=====================================================
Increase in cost of construction materials: A challenge to overcome
By
Sourav Dutta
Manager-Civil
Ion Exchange India Limited
Manager-Civil
Ion Exchange India Limited
Construction industry at present is facing a major hike in material price, especially cement, sand and stone chips. The following document is prepared to highlight the reduction in concrete manufacturing cost upon using Fly Ash (BIS3812). The method of mix design has been done in reference with BIS10262-2009. Hope that any contractor over India will benefit from the given working and follow the suggested method to reduce their construction cost.
This will have the following advantages: (1) Reduction in use of construction materials which are facing scarcity now-a-days, (2) Reduction of construction cost for contractor, (3) Use of fly ash in a effective manner, which are generated as waste product from thermal power plants and various industrial plants, (4) Assisting in scientific disposal of waste product from thermal power plants and various industrial plants.
Assumed parameters for RCC M25 per Cum mix design as per IS10262:2009 :
Exposure= Moderate
Quality control at site= Fair
Method of concrete placing= Pumping
Grade of cement= 43
Grading zone of sand= Zone 2
Type of aggregate= Saturated surface dry aggregate
Nominal maximum size of aggregate= 20mm
Chemical Admixture (IS 9103)= None
Exposure= Moderate
Quality control at site= Fair
Method of concrete placing= Pumping
Grade of cement= 43
Grading zone of sand= Zone 2
Type of aggregate= Saturated surface dry aggregate
Nominal maximum size of aggregate= 20mm
Chemical Admixture (IS 9103)= None
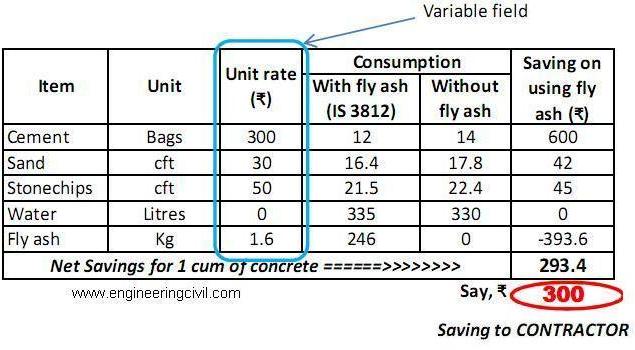
Assumed parameters for RCC M30 per Cum mix design as per IS10262:2009 :
Exposure= Severe
Quality control at site= Fair
Method of concrete placing= Pumping
Grade of cement= 43
Grading zone of sand= Zone 2
Type of aggregate= Saturated surface dry aggregate
Nominal maximum size of aggregate= 20mm
Chemical Admixture (IS 9103)= None
Exposure= Severe
Quality control at site= Fair
Method of concrete placing= Pumping
Grade of cement= 43
Grading zone of sand= Zone 2
Type of aggregate= Saturated surface dry aggregate
Nominal maximum size of aggregate= 20mm
Chemical Admixture (IS 9103)= None
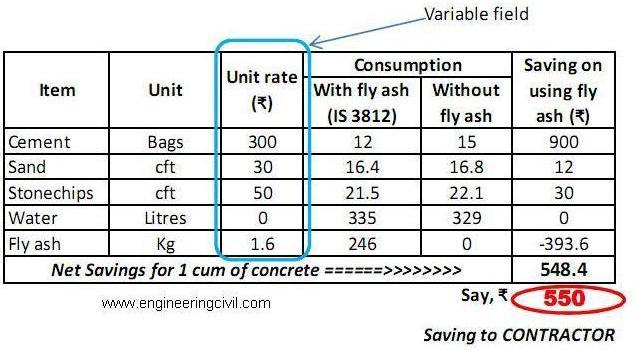
Increase in cost of construction materials: A challenge to overcome
Posted in Civil Engineering Information |
By
Sourav Dutta
Manager-Civil
Ion Exchange India Limited
Sourav Dutta
Manager-Civil
Ion Exchange India Limited
Construction industry at present is facing a major hike in material price, especially cement, sand and stone chips. The following document is prepared to highlight the reduction in concrete manufacturing cost upon using Fly Ash (BIS3812). The method of mix design has been done in reference with BIS10262-2009. Hope that any contractor over India will benefit from the given working and follow the suggested method to reduce their construction cost.
This will have the following advantages: (1) Reduction in use of construction materials which are facing scarcity now-a-days, (2) Reduction of construction cost for contractor, (3) Use of fly ash in a effective manner, which are generated as waste product from thermal power plants and various industrial plants, (4) Assisting in scientific disposal of waste product from thermal power plants and various industrial plants.
Assumed parameters for RCC M25 per Cum mix design as per IS10262:2009 :
Exposure= Moderate
Quality control at site= Fair
Method of concrete placing= Pumping
Grade of cement= 43
Grading zone of sand= Zone 2
Type of aggregate= Saturated surface dry aggregate
Nominal maximum size of aggregate= 20mm
Chemical Admixture (IS 9103)= None
Exposure= Moderate
Quality control at site= Fair
Method of concrete placing= Pumping
Grade of cement= 43
Grading zone of sand= Zone 2
Type of aggregate= Saturated surface dry aggregate
Nominal maximum size of aggregate= 20mm
Chemical Admixture (IS 9103)= None
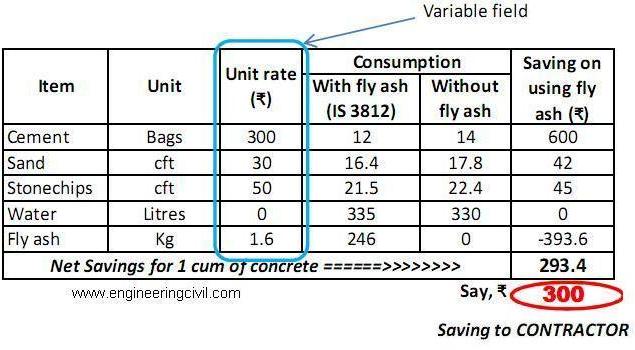
Assumed parameters for RCC M30 per Cum mix design as per IS10262:2009 :
Exposure= Severe
Quality control at site= Fair
Method of concrete placing= Pumping
Grade of cement= 43
Grading zone of sand= Zone 2
Type of aggregate= Saturated surface dry aggregate
Nominal maximum size of aggregate= 20mm
Chemical Admixture (IS 9103)= None
Exposure= Severe
Quality control at site= Fair
Method of concrete placing= Pumping
Grade of cement= 43
Grading zone of sand= Zone 2
Type of aggregate= Saturated surface dry aggregate
Nominal maximum size of aggregate= 20mm
Chemical Admixture (IS 9103)= None
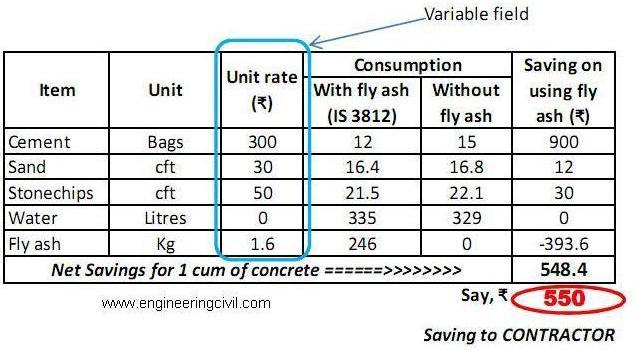
No comments:
Post a Comment